IS A PRESS CHECK NECESSARY?
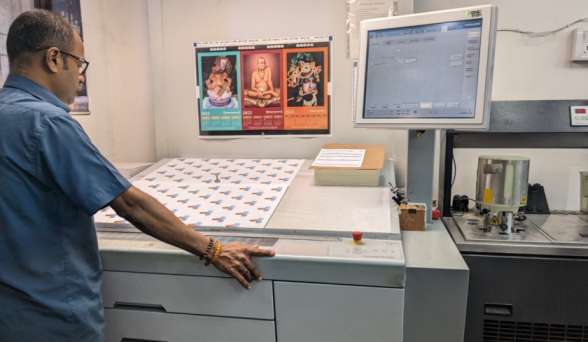
For years, the press check was a standard part of commercial printing. You’d finalize a design, approve the proof, then head to the printer to spend hours checking press sheets before giving the OK. It was a necessary but time-consuming step in ensuring a successful print run, especially before today’s advanced color assessment tools.
Thankfully, those days are mostly in the past now.
So, how can companies trust printers to ensure the final product matches the proof without them being there? It’s a simple mix of:
1. Industry standards that didn’t exist before.
2. Technology that can judge accuracy and quality without human intervention.
The result is just as simple:
You’ll spend less time picking at the little details of a project, and you’ll get a high-quality print that matches your proof every time.
To understand why the press check is no longer needed, let’s take a quick look at what press checks used to be like and explore the standards and technology that have replaced this time-consuming task.
WHAT IS A PRESS CHECK?
In the past, after approving a proof but before starting the presses, a few company representatives would visit the printer for a final press check to ensure everything looked good. If any issues arose, they’d collaborate with the pressman to fix them before starting the presses.
However, this process wasn’t always straightforward. Differences in opinions, poor judgment, and other issues could prolong the process for an entire day and sometimes lead to a subpar final product, depending on who was involved.
Today, press checks are much less common, thanks to recent advancements in printing standards and technology.
In the past, each printer had its own standards, leading to significant variations between print shops. However, newer industry-wide standards have been adopted, providing companies with consistent quality regardless of the print shop they use.
One notable standard is the GRACoL standard, which ensures consistency from proof to final product. As a result, the need for press checks has been greatly reduced for the majority of projects.
HOW DO STANDARDS LIKE GRACOL ENSURE A QUALITY PRINT RUN?
GRACoL is a standard used to measure color consistency in printed products. When looking for a top-notch commercial printer, keep an eye out for G7 Certification. This certification ensures that the printer not only understands GRACoL but also has the necessary tools to implement it effectively. Essentially, G7 provides a reliable way for those seeking commercial printing services to establish trust and quality assurance from the start.
HOW DO TODAY’S TOOLS AND OPERATING PROCEDURES DO THE CHECKING FOR ME?
Before printing plants had the fancy color tools they do now, matching the proof to the press sheet was done by eye. But humans aren’t perfect, so this way was kinda subjective.
Nowadays, computers can do it much more precisely using a scientific system that follows professional standards.
Before printing, each press sheet is checked to make sure it matches the proof you approved. At Suttle-Straus, we calibrate each device to make sure everything stays within the right limits. Plus, we regularly test each press to make sure it’s accurate according to the GRACoL standard.
With these checks in place, it’s up to us to make sure your final product matches the proof. This means you’ll always get what you asked for, with the same level of quality every time.
At One Step Print LLP, we’re all about building strong partnerships with our clients. Curious about the types of projects we excel at? Click here to explore our services. Plus, don’t forget to subscribe to our newsletter for exciting updates and valuable printing insights! Subscribe now to stay in the loop.